Warco Bandsaw Manual
Posted By admin On 02.10.19
I have the Axminster power hacksaw, but if I was buying it again I would get it from Arc, it is much cheaper, even after adding the carriage. Exactly the same machine except for the colour. It cuts reasonably fast, exactly square, and the blades seem to last forever. It does really need a mod doing before using.
- Have defective. Do not clean the saw band whilst it is in motion; 6) Wear suitable personal protective equipment, when necessary, this could include.
Because the air strut is fairly strong, it doesn't allow the blade to cut as heavily as it should. I modded mine by putting an adjustable weight so I could regulate the downwards force more accurately. It is NOT a machine for lifting up and down, it took two of us to lift it onto the bench, but it does have a fairly narrow footprint, and that allowed me to tuck it fairly tight into a corner. It is a difficult choice for you to make, and really only you can decide. We can tell you the pros and cons, but it is your money that is being spent. The MCB100a can also be used as a vertical band saw if you make a table for it. I've not done that yet for mine.
- Apr 09, 2013 Warco 314 bandsaw spares. I phoned Warco spares department and explained what I wanted. All Forum Topics > Manual machine tools > Warco 314 bandsaw spares.
- Machinery Locator: Used and new machine tools for sale in Category: Sawing. Horizontal bandsaws. This fully automatic roller fed bandsaw is equipped with many useful.
If you do, make sure it's bolted down - it WILL be unstable otherwise. The biggest problem I have with mine is getting the cutoff adjusted properly. There's a collar, grub-screwed on the hinge, which activates the cutoff switch. I've not been able to get mine to work properly so far - it either runs on, or stops too early. So I've set it to run continuously and I keep an eye on it and manually stop it when it's done.
WRT weight: I can lift the MCB100 on my own, but I do make sure where it's going is clear first! Lots of saws available 2nd hand, I'd be inclined to buy whatever was near me and well priced.
For a home workshop though I'd err towards the hacksaw, simple, cheap, not much to go wrong and blades available from B&Q (if you're desperate). If you do a lot of cutting then a bandsaw is faster. Finally, cheap bandsaws are more of a risk than cheap hacksaws. (out of the two links you show, I'd buy the bandsaw.
But look around for 2nd hand. I paid £50 for a decent hacksaw with a lifetimes supply of blades). I have a cheep bandsaw. I buy quality blades for it and keep the guides adjusted so It cuts square. The saw has three speeds.
In my home shop I'm not in a hurry. I've never taken it off the slow speed. I use my saw a lot! The last blade probably lasted over a year.
I always keep an extra on the wall so If one breaks on Sat afternoon I won't be without a saw the whole weekend. No experience with A power hacksaw. I almost bought one that was a hundred years old a few weeks ago.
Warco Bushing
But I'm running out of room in my shop and I have enough projects. Power hacksaws are simpler mechanism-wise. Bandsaws are more complicated mechanism-wise. The (relatively) cheap Chinese drop-bandsaws suffer from the same 'quality workmanship' that other Chinese product suffer. However, that said, there are steps you can take that will rectify that situation at a fairly low cost.
The main index & clamp area of the saw is rarely flat. A trip to the milling machine solves this easily. The index angle is neither square nor well-fit to the pivot. A trip to the milling machine and some boring (replacing the poor screw pivot with a shoulder screw) solves this easily. The pivot bar about which the saw itself pivots is rarely parallel to the table - making the saw cut at a non-90° angle. Reboring the pivot holes and installing bushings solves this relatively easily (you may have to add material to the base).
The blade guide ball bearings are often of 'less than acceptable quality.' (I paid $12 for 4 good quality ball bearings.) I got a 'deal' on my first purchase of a Harbor Freight drop bandsaw back in the mid-1980's as something had punched a hole through the base. Luckily, I am good friends with a 'magician caliber' welder who repaired the broken area for beer.
I made the repairs noted above. Using good blades (I will only use Starrett blades), I can cut a 4' X 6' piece of steel bar and have a 63 micro-inch finished surface that is flat within.004 FIM and square to the two index surfaces within.004 FIM - it is just a very slow cut. I have reworked several (8-10) such saws in the intervening years. Were I billing my time at commercial rates, it would not really be worth it (i.e. It would be cheaper just to go out and buy a really well made saw). However, if sweat is less dear than cash, a good bargain may be had.
Warco Bandsaw
I probably spent 25-30 hours getting my first saw up and running properly. Recent efforts have been completed in 6-8 hours on average. Also, I threw away that miserable excuse for a table that comes with such saws and made a plywood on to replace it. The plywood one is longer (with outrigger supports) and has more useful fences that I power with air cylinders for untended cutting (don't apply more than 15-18 lbs of force to the operation on such a light saw). Half-inch (1 cm) nominal X 6' (150 mm) stroke air cylinders show up in 'recycling yards' quite regularly around here for $5. Creative application of C-clamps, CA adhesive, and some pieces of angle iron make this an amazingly useful addition. It takes (about) 10 hours to make a 6' long cut in 3' thick steel plate, but I can let it run overnight!
Warco Machine Tools
FYI: I get about 150-200 hours of cutting out of a $13 Starrett blade (barring stupidity such as unclamped cuts that bind and break a blade). I recently bought myself a band saw, just like the B1180 at the bottom of this page My first impressions are not good. The machine looks like it has been assembled by a child. Screws are screwed in at such an angle that they loook as if the were beaten in place.
All screws are of the lowest quality you can get your hands on (4.8), and several are already bent despite the saw rarely having been used. There is at least 10mm of axial play in the vise tightening screw. Then comes the hydraulic lowering of the blade. The needle valve which sets the down-speed has no dial or way of showing what speed you have set it at, or at least to find the same speed as the last time.
Anyhow, when you eventually have found a suiting speed and set it at that, the saw will stop lowering itself after a while. But when you try to adjust the ultra sensitive valve, the blade suddenly drops onto the workpiece, jamming the blade. The blade is now also junk. But I hope that with a bit of work, I will make the saw better than new. Watch out for a new project. Jason, Although I didn't mention it before, it seems that this hacksaw doesn't lift the blade on the return, non cut, stroke. So when the first end wears out, (it only strokes half the length of the blade), turn it around and use the other end.
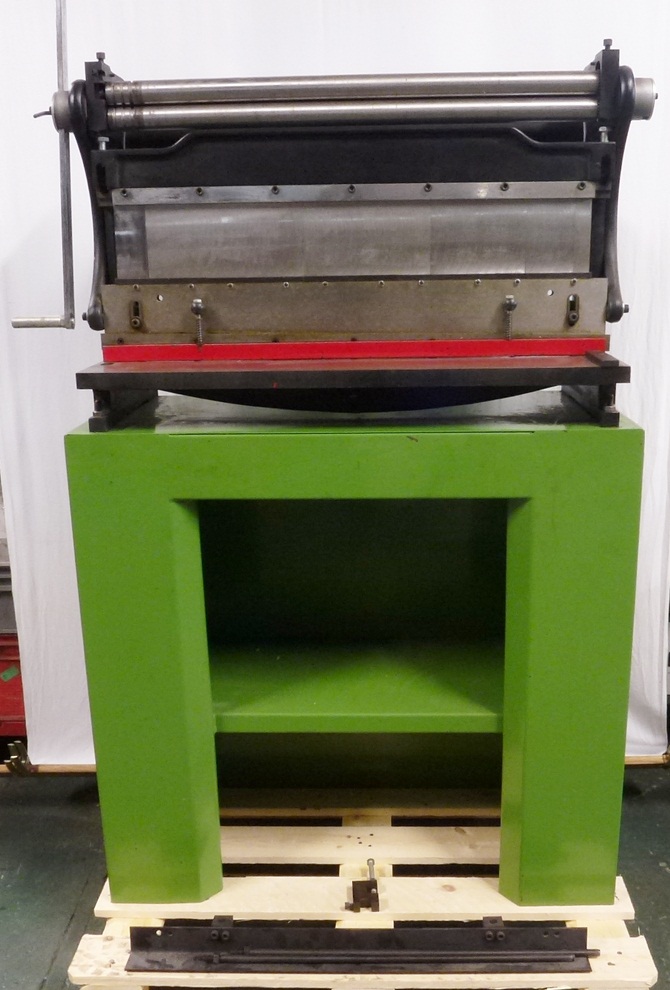
I would expect a blade to last at least a year, maybe a lot more, depending what you are cutting and how often. Mine lasted over 2 years, with a fairly heavy cutting regime, and even then it wasn't completely knackered. I just hope that you think you have made the right choice. BTW, I did make another mod that I forgot to tell you about.
Mine came with brass grease nipples, which I hate, because they can snap off fairly easily, especially if you use a good gripping grease nozzle. I fitted mine with steel ones, just for peace of mind.
CY90 Bandsaw Mitre Arm Saw Ideal for the smaller workshop, these bandsaws are built to last. Features mitre arm 45° swivel. Material held firmly in a leadscrew operated vice.
Arm swivels across material at angles from 0°-45 - which avoids the arc area associated with a conventional mitre vice. Supplied complete with a 14tpi (general purpose) flexible carbon blade. Now includes an additional Sheffield made blade for no extra charge! Specification Cutting capacity 90° O 90mm Cutting capacity 90° ▀ 90 x 130mm Cutting capacity 45° O 65mm Cutting capacity 45° ▀ 90 x 65mm Blade speeds 20 / 30 / 50 m/min Blade size 12.7 x 0.5 x 1300mm Drive Vee belt Tranmission Sealed worm gear Power 240v / 1PH Motor 400w Weight 41kg Dimensions (Measurements taken to end of handle grips) Height to bed 630mm Height 710mm Width 255mm Length 710mm (865mm with arm raised) Price includes VAT and UK mainland delivery.
Product download.